FormBox: pro inženýry a průmyslové designéry
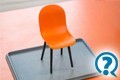
![]() E-booky zdarma |
![]() Školení v oblasti CNC frézek |
![]() ESD inspekce |
Případové studie pro inženýry a průmyslové designéry
Zkrácení doby výroby prototypu obalu pomocí FormBoxu a 3D tisku
- vývoj produktu redukován ze 3 měsíců na dva dny
- ušetřeno 1000 GBP za projekt
Úvod
UTR (Under the Roof) Decorating je kanadská společnost vyrábějící nářadí. Vyvíjí, testuje, vyrábí a dodává do maloobchodů po celém světě inovativní řadu produktů pro domácí dekorování. Tým UTR vytváří ve své vlastní laboratoři pro inovaci produktů širokou škálu kutilských produktů inspirovaných problémy pozorovanými při práci v terénu.
UTR používá FormBox k prototypování svých designů blistrových obalů. Celá řada produktů UTR je balena v blistrech s podložkou. Pomocí FormBoxu a transparentních forem Cast Sheet je tým schopen replikovat hromadně vyráběné bristry, aniž by opustil interní dílnu. Mají také dvě 3D tiskárny, které se používají k vytváření prototypů blistrových obalů. Využití kombinace 3D tisku a vakuového tváření umožňuje týmu rychle vytvářet nové designy a testovat je s uživateli a potenciálními zákazníky.
"S FormBoxem kombinovaným s 3D tiskárnami jsme dokázali zkrátit dobu vývoje našich oblalů z týdnů na doslova dny." - Under The Roof
Problémy
Zatímco UTR navrhuje všechny své produkty v Kanadě, fyzicky jsou vyráběny v Číně. V minulosti musel nechávat vyrábět v Číně také všechny své prototypy. Fyzické a kulturní rozdíly mezi Kanadou a Čínou někdy způsobovaly zpoždění vývojové fáze. Odesílání prototypů z Číny do Kanady bylo časově náročné, nákladné a vystavovalo je potenciálnímu poškození během přepravy.
Při vytváření nových produktů je důležité zjistit, kolik jednotek mohou někteří maloobchodníci zvažovat za první objednávku. UTR pak může dělat přesné odhady, kolik jednotek by si měli objednat z továrny v Číně. Čím lepší kvalita modelu je pro tyto maloobchodníky k dispozici, tím vyšší je počet jednotek, které musí objednat, což zase zlevňuje jednotkové náklady UTR.
Řešení
Díky vlastní výrobě všech obalů pomocí 3D tiskárny a FormBoxu nevznikne při přechodu od myšlenky k fyzické formě žádná šance na chyby. Tím se zcela odstranila potřeba prototypování v Číně a snížilo se riziko poškození při přepravě, zpoždění nebo nákladných chyb. Po zavedení procesu FormBox + 3D tisk společnost UTR zkrátila dobu realizace vývoje obalů z průměrných tří měsíců na pouhé dva dny.
Použití Cast Sheets umožnilo UTR vytvářet téměř přesné jednotlivé repliky navrženého blistru. Pomocí nich, určených jako ukázkové příklady nových produtků, mohli maloobchodní kupující přesně odhadnout, kolik objednávek může továrna vyrobit.
Výsledky
- výrazně zkrácená doba vývoje produktu
- zvýšené objednávky od maloobchodníků
- nižší náklady na lepší vzorky
- schopnost vytvářet kvalitní vzorky
Vývoj prototypů a krátkých sérií produktů s 3D tiskem a formami z FormBoxu
- doba vývoje produktu snížena na tři dny
- úspora 190 GBP za náklady na nastavení
Úvod
Dean Pankhurst je interdisciplinární designér, který pracuje v různých médiích, ale hlavně v produktovém designu a digitálních médiích. Pracuje v produktovém týmu společnosti Mayku a zároveň navrhuje a vyrábí pro umělce a designéry jednorázové akce, prototypy a malosériovou výrobu. Má přístup k řadě nástrojů a strojů a díky FormBoxu rozšířil škálu možností, které může svým klientům nabídnout.
Dean před několika lety dostal nápad na stmívací lampu a pomocí 3D tisku a FormBoxu jej nedávno přetvořil ve skutečnost. Obecná myšlenka je, že žárovka funguje také jako stmívač, který nastavuje jas lampy. Vnitřek výrobku tvoří vysokonapěťová deska s obvody, která má potenciometr a několik velkých kondenzátorů.
"FormBox doplňuje všechny ostatní nástroje, která mám k dispozici, což mi umožňuje s jistotou vyrábět celý produkt sám, a to nákladově efektivním a flexibilním způsobem." - Dean Pankhurst
Problémy
Dean chtěl, aby byl exteriér lampy vyroben z těžkého odlitého materiálu, který bude vypadat jako texturovaný kámen. Tento druh přírodních povrchových úprav nemůže být 3D tiskárnou proveden přesvědčivě. Požadované těsné tolerance však znamenaly, že ruční řezbářství nebo soustružení také nebude dobrou volbou.
Dean dále potřeboval zajistit, aby všechny části do sebe správně zapadly. Teprve poté se mohl rozhodnout pro konečný návrh. Testování tolerancí a celkového tvaru konstrukce pomocí odlévacího procesu, např. pomocí silikonu, by bylo neúprosně nákladné. Vytvrzování silikonových a polyuretanových forem navíc trvá velmi dlouho. Při vývoji nových produktů je důležité rychle iterovat a co nejdříve pokročit v prototypování, abyste se na trh dostali co nejrychleji. Čekání 24 hodin na vytvrzení velmi zpožďují celý proces.
Řešení
Použití litých materiálů vám umožňuje otestovat jemné rozdíly ve struktuře a barvě a zároveň kombinovat přesnost a opakovatelnost digitální výroby s hmatatelnějšími a vysoce kvalitními povrchovými úpravami. Zahrnutí FormBoxu do procesu návrh umožnilo Deanovi rychle vyrobit formy pro testování i finální výrobu stmívací lampy.
FormBox je neuvěřitelně užitečný pro výrobu forem pro prototypování odlitků. Dean se snaží použít vakuové tváření, kdykoli je to možné, protože se sníží náklady na práci ve srovnání s jinými procesy výroby forem, jako je silikon nebo polyurethan. Dean potřeboval zajistit, aby do sebe všechny součásti zapadly správně, a zároveň neměl tak vysoký rozpočet, aby mohl dlouze testovat tolerance a celkový tvar konstrukce pomocí nákladného procesu odlévání.
Šablony pro formu byly vytištěny na 3D tiskárně a vytvořeny pomocí Cast Sheets za méně než jeden den. Dvoudílná forma umožňuje dutý tvar s otvory pro žárovku a okrajem na základně pro elektroniku. Dean vyrobil několik prototypů ze sádry a standardního jesmonitu AC100, čímž otestoval celou sestavu. Nakonec pro finální produkt zvolil jesmonit AC730 v uhlíkové šedé.
FormBox doplnil všechny ostatní nástroje, které má Dean k dispozici, čímž mu umožnil s jistotou vyrobit celý produkt sám. Navíc nákladově efektivním a flexibilním způsobem.
Výsledky
- schopnost dosáhnout přirozených povrchů pomocí nástrojů pro digitální výrobu
- významné snížení nákladů na prototypování
- zkrácení doby vývoje projektu
Rychlé prototypování s FormBoxem
Theo Ford je oceňovaný londýnský průmyslový designér. Vytváří produkty pro klienty a potřebuje postupovat rychle a držet tak krok s jejich plánováním. Theo provozuje malou dílnu a musí udržovat nízký rozpoačet. Má malou modelářskou sestavu s 3D tiskárnou, FormBoxem a dalším základním prototypovým vybavením.
Pomocí FormBoxu může Theo Ford za pár hodin přejít z CAD programu až k dávce fyzických prototypů. Díky tomu může ukázat svům klientům své vize, a to za minimální náklady. Kombinací 3D tisku a vakuového tvarování je Theo schopen za jediný den hromadně vyrobit řadu prototypů.
Theo navíc utratí pouhou 1 GBP za každý prototyp židle, který vytvoří pomocí FormBoxu. Z rozpočtu jeho klienta by byla outsourcingová výroba neúnosně nákladná.
"FormBox je v mé dílně mocný nástroj. Ve spolupráci s mojí 3D tiskárnou dokážu vyzkoušet různé varianty bez nutnosti dlouhého tisku nebo nákladného outsourcingu výroby." - Theo Ford
Problémy
Theo byl požádán novým co-workingovým prostorem o návrh sady zakázkového nábytku pro novou lokaci v Londýně. První výzvou bylo vytvoření sady židlí, které by odpovídaly skandinávskému stylu. Rozpočet byl napjatý a klient byl velmi konkrétní. Theo chtěl svůj nábytek vymodelovat, aby klientovi mohl svou vizi přednést.
Řešení
Nejprve vytvořil barevné schéma a návrhový jazyk pro prostor, potom začal s náčrtem variací. Theo chtěl pro klienta vymyslet několik nápadů a materiálních úprav. Časová a rozpočtová omezení znamenala, že tisk 10 variant židlí nebude možný. Své nápady tedy navrhl ručně a vymodeloval formu židle v Solidworks. Potom pomocí své 3D tiskárny vytvořil hlavní šablonu. K provedení několika variací svého designu využil FormBox.
Theo rychle zhotovil 10 identických kopií skořápky židle, vyřízl je skalpelem a každou nastříkal jinou barvou. Na několika kusech použil texturizační základ. Experimentoval s matnými a lesklými povrchy a vyzkoušel různé odstíny barev a tloušťky materiálu. Dále Theo vytiskl jednu sadu nohou, aby mohl předvést návrh židlí v celé jejich krásné. Klient přišel do studia a ihned byl na Theově zmenšeném modelu prostoru schopný vidět, jak různé povrchové úpravy fungují. Společně se rozhodli pro barevné schéma a stanovili kolektivní směr designu sady židlí.
Výsledky
- 10 různých variant židlí za minimální časové a finanční náklady
- rychlá vizualizace designu
Kategorie produktů
![]() |
Vakuové formovací stroje |
![]() |
Termofólie |